The UEFA Euros Championships 2024 this summer saw asome thrilling action in stadiums across Germany. But what fans might not have noticed is the roofing structures which protected them from the elements. But come rain or shine it is the membrane roofs of these venues that keep the fans comfortable and in a sustainable way.
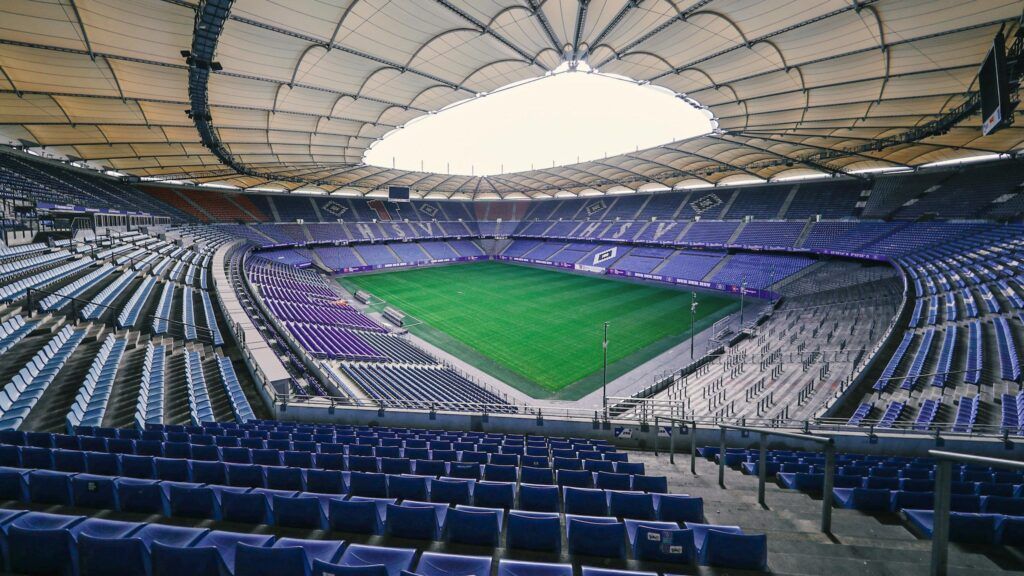
The VolksparkStadion in Hamburg, home to Bundesliga club Hamburger SV, was completely renovated before the start of the European Championships and a new membrane roof cover was fitted.
“We’re doing a good number of refurbishment jobs at the moment,” said Thomas Hermeking, head of preconstruction at Pfeifer Structures. “We have just done the membrane exchange on Hamburg’s VolksparkStadion which is in use now for the European Championships.
“It’s a membrane covered cable net structure that we installed about 26 years ago. The PVC membrane had reached the end of its lifespan and had to be changed. The cable net itself, however, is still in good shape and will live on, probably for a minimum 30 more years or so without doing anything to it.
“The owners wanted a PVC cover again. Materials have improved over the last 25 years and there has been improvement in their durability. In most cases, it’s not about actual lifespan of materials anymore, it’s about how long customers want to use the buildings for and the way they want to use them.”
Independent consulting engineers and designers Schlaich Bergermann partner said the roof of the VolksparkStadion spans the entire spectator area of the completely renovated 55,000 seat stadium.
The primary structure of the roof consists of a pre-stressed cable system with 40 radial cable girders. The girders are connected to an inner cable tension ring and to 40 steel masts located behind the grandstand around the stadium. The steel structure weighs 2,300t and the cables 460t.
The masts carry the outside compression ring which completes the typical spokes wheel structure, which was also used for the previous roof.
The span of the cable truss and the roof depth is up to 72 metres. The roofing is made up of 35,000m2 of a PVC-coated polyester membrane, held by a secondary structure in a double-curved shape.
Hermeking said that four years ago Pfeifer Structures had also carried out the same renovation work on MHPArena in Stuttgart, which is also in play for the Euros.
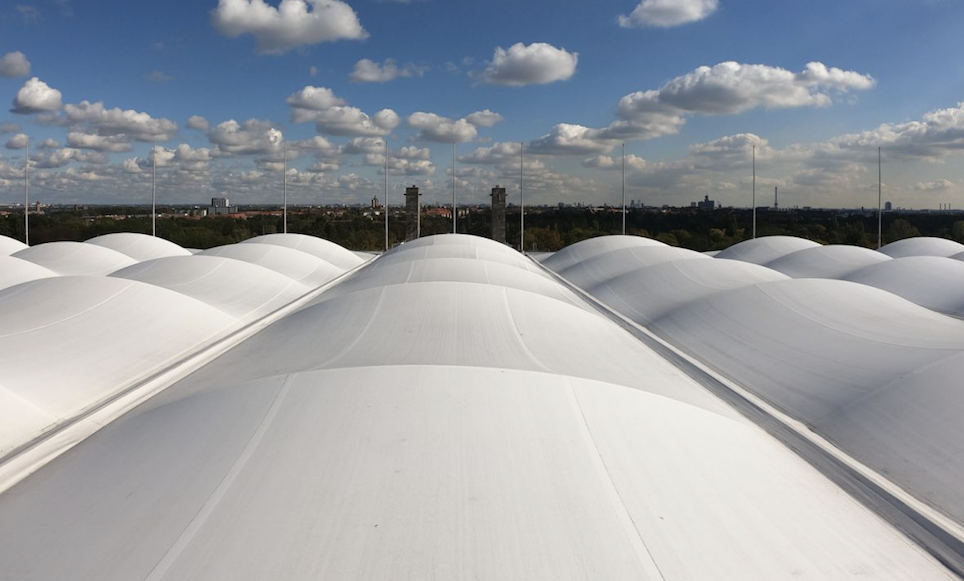
Pfeifer Structures, which was responsible for the enormous roof of the NFL SoFi Stadium in Los Angeles, California, is also involved with work on the Grand Stade de Tangiers in Morocco and with projects in Saudi Arabia.
He added: “For the Grand Stade de Tangiers in Morocco we’re responsible for doing the complete envelope – the roof and façade in membrane. It is an existing site and the stadium is getting a complete overhaul. The old, partial steel roof has been dismantled already. Our new roof will be put on in cooperation with a local steel contractor and work is expected to complete in mid 2025.”
The roof will consist of 40,500m2 of PTFE membrane and the stadium’s façade will be encased in 42,000m2 of PVC mesh.
Environmental benefits
Membrane has helped to change the way the construction and architecture sectors think about building stadiums, allowing for more versatile and more environmentally friendly ways to construct or adapt major sporting venues.
The use of membrane provides a welcome solution to some of the construction industry’s toughest environmental challenges while at the same time offering unique visual character.
According to some studies, the construction industry accounts for 50% of climate change. The use of concrete has a large part to play in this, itself accounting for up to 8% of global CO2 emissions.
Because membrane is lightweight as well as durable, the buildings enveloped with it do not need the same deep and heavy concrete foundations or steel structures to support them.
Membrane has a lower carbon impact when compared to polymer-based alternatives such as a polycarbonate canopy.
Hermeking said: “The combination of a cable net structure and membrane is the lightest option for a roof. It gives the lowest weight per square metre and saves all the money of the concrete which would also have the highest impact on the project’s carbon footprint.
“It’s also about timing because these are quick to erect and when the roof is up there’s freedom to work on the rest of the stadium underneath.”
Adam Mandrysz, COO of Hightex Maintenance, which has a wealth of experience in the fabrication and maintenance of membrane roofs and has been involved with projects including the retractable roofs on Wimbledon’s Centre Court and Poland’s National Stadium among others, added: “With the use of membrane, the energy needed to implement the structure is relatively low and emissions are lower. Transportation costs are also lower because you can fold all of the lightweight material. With proper maintenance you can use it for 40 or 50 years. At the end of its lifespan, you can use the structure again and install a new cover.”
Hightex’s most significant recent project was the fabrication and installation of 180,000m2 of installed ETFE membrane for the iconic Al Bayt Stadium in Qatar for the 2022 FIFA World Cup.
ETFE also offers free lighting. It transmits 95% of light giving 500lux daylight needed for indoor sports, avoiding the need for intensive daytime electric lighting. This is also enough light for plants to grow, so it is ideal for stadiums with grass pitches.
In certain cases, membrane can also be recycled at the end of its lifespan.
Hermeking added: “In the case of the old membrane from the VolksparkStadion we have managed to bring it into a recycling loop. Membrane always consists of two base materials – the yarn and the coating. The coating is a chemical mixture of several things, so you split these two materials. You create granulates of the coating which you put in another process and then you use the yarns to make different kinds of fabrics.
“In terms of sustainability at Pfeifer, we’re on our way to completing all our environmental product declarations (EPD). We started with our ETFE systems and foils so that we can publish what impact our products and the use of them has on the environment. We’re continuing with our cable systems and will also do that for the rest of the membrane materials.”
Maintenance is key
In 2004, Bavarian membrane pioneers, Hightex, installed a membrane roof onto the brutalist venue built for the 1936 Olympics to give it a new lease of life and protect spectators from the weather.
The roof of the stadium is designed as a light cantilevering steel construction with an upper and lower membrane. The total length of the steel trusswork functioning as the main support is estimated at 68 metres and is visible through the translucent membrane.
With proper care and regular maintenance, the membrane structures, which consist of ETFE (ethylene tetrafluoroethylene) or PTFE (polytetrafluoroethylene) are still in fantastic condition.
Hightex, which has recently changed focus to purely membrane maintenance after more than 30 years producing and installing membrane projects all over the world, worked its crew hard in the run up to the Euros, making sure the roof is in peak condition, patching any holes and tears in the material which have developed since their last inspection.
Liam O’Connor, Training Manager at Hightex Maintenance, stressed the importance of carrying out this regular care and maintenance to keep the materials in tip-top shape.
“I treat it like it’s a skin. If you look after your skin then the rest will be OK,” he said.
“Originally these structures were given a lifespan of 30 years, but we’ve been looking after a couple of roofs which are over 30 years old and still in fine condition.
“All this started in the 1990s and a lot of these roofs are now supposed to be coming to the end of their lives, but if they’re properly looked after they could keep going for another 10 or 15 years. Nobody really knows because membrane as a working material has really only been around since the 1990s.”
O’Connor explained how a typical maintenance programme, which is usually carried out twice a year, works.
“We’re looking for holes, we’re looking for scratches, we’re looking for damage caused by other companies working up on the roof. We document everything, photograph it and repair it.
“You get third parties up on the roof looking after their satellite dishes or their antennas or their cabling or motors and they tend to cause small amounts of damage and unfortunately they do make holes in it.”
Human error isn’t the only problem O’Connor has to deal with, though.
He added: “Then the crows come along and they pick at the material and make the holes bigger so a lot more water gets through. But we’ve got that under control because we come here twice a year now.”